Global Events
Hygienic welding of stainless steel tubing in the food processing industry | New available guideline
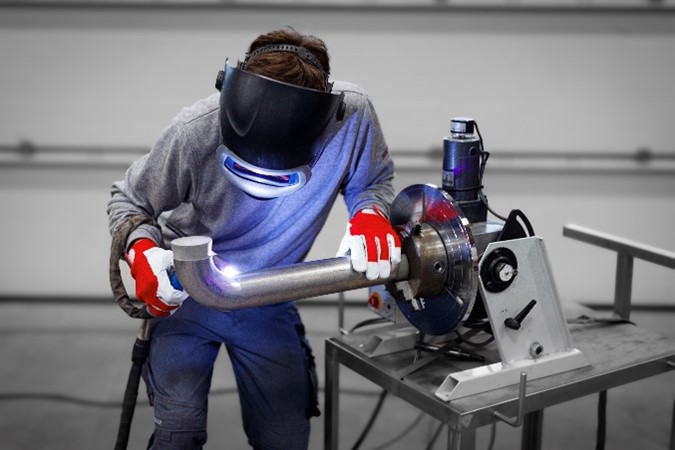
Now available in our catalogue
Another milestone for this year: the release of EHEDG Guideline 35, 'Hygienic welding of stainless steel tubing in the food processing industry', which provides information on how to achieve hygienic welds, gives a basic understanding of important operating procedures, and also offers information on how to test and verify the systems.
This updated guideline provides a comprehensive overview of what constitutes a hygienic weld and specifies the technical requirements for achieving on-axis hygienic (sanitary) welding between tube segments or between a tube and control components like valves, flow meters, or instrument tees.
Focused exclusively on GTAW (TIG) welding methods, this document covers both autogenous welds without filler material and welds with filler material. It mainly addresses the surface of the weld in contact with the finished or intermediate product.
We asked the Chair of the the Working Group Welding, Peter Merhof (GEA) the following question: Some say that ‘less is more’ when it comes to avoiding hygienic design risks in food processes. Does this apply to welding?
'There is a belief that 'the best weld is no weld,' but with current technology, it is possible to achieve high-quality results due to precise preparation methods. This principle was a key focus in revising the new guideline. We emphasised the importance of proper preparation and included examples to illustrate it. This approach helps those who need to meet high-quality standards. In our experience, companies sometimes place orders without detailed specifications, which complicates the assessment of weld quality. Clear specifications are crucial, and those who use or refer to our guidelines find that it simplifies the process for both customers and suppliers.'
A special thank you to the team of professionals who contributed to this important revision: Martin Barnickel (LVFZ), Thomas Kopitzke (Encoma GmbH), Peter Merhof (GEA), Kees Meurs (Polysoude), Georg Slavik and Thomas Feldmeier (STW – Sensor Technik Wiedemann GmbH), Dr. John Wahlers (Stream Engineering Solutions Ltd.) and Patrick Wouters (Cargill).