EHEDG starts testing open food processing equipment
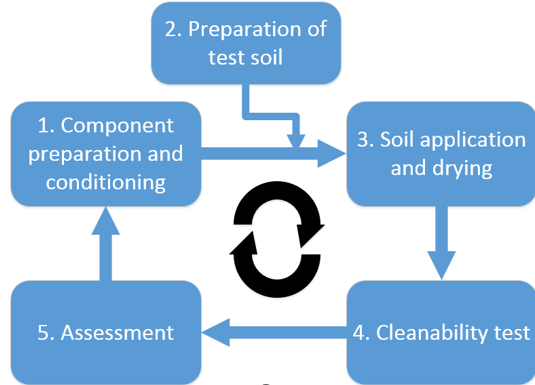
Where technology meets food industry needs
EHEDG developed a new test method to reliably assess the external design of open food processing equipment. This new EHEDG Open Plant Cleaning (OPC) test method brings the benefits of EHEDG certified equipment within reach of food industries that process their food in open plant environments, such as meat, fish, and bakery companies. This method will enable food processing equipment developers to optimise their designs and support open food processing companies to mitigate food contamination risks.
Across the globe, major food and beverage companies rely on EHEDG certified components to ensure the effectiveness of their cleaning-in-place efforts. By choosing EHEDG certified components, they optimise food safety, food quality, productivity, and sustainability of their closed food processing environments. The new OPC test method will also enable companies that apply equipment in open plant cleaning settings to assess the real world cleanability of their components exposed to exterior surfaces. Ultimately, the launch of this new OPC test method is also exciting news for food equipment component producers who supply open plant processing clients and want to obtain competitive advantages for their innovations.
Where technology meets food industry needs
EHEDG developed the new OPC test method in collaboration with Fraunhofer Institute IVV (Germany), to comply with repeated requests by EHEDG Company Members for such a testing method. Since the method involves the use of a robotic arm, it currently allows EHEDG Authorised Testing Laboratories to test the external design features of machinery components with dimensions up to 0,6 x 0,6 x 0,6 m³. The first three EHEDG Authorised Testing Laboratories in Germany, France and Spain that offer the EHEDG OPC test method are willing to size up their testing capacity as soon as more requests to test bigger components start coming in.
Challenge of complexity
If there’s such a need for open plant cleaning tests, then why didn’t EHEDG develop such a method much earlier? Marc Mauermann, Deputy Director at Fraunhofer Institute for Process Engineering and Packaging IVV Dresden: ‘Developing a cleaning test method to assess the external cleanability of components proved to be a very complex undertaking, particularly because of the many test-result determining aspects involved, like the fluid dynamics, and the sheer variety of external surface designs. EHEDG tests typically consist of three stages: a soiling stage, a cleaning stage, and a cleaning validation stage. For this new test method, we had to approach these stages in completely new ways.’
Max Hesse, Group Leader Machinery and Process Development at Fraunhofer IVV: ‘If you design a test method for closed systems, the system boundaries define themselves just by the shape of the components that are being tested. So, when testing a pump for example, you apply pressure and adjust the mean velocity of flow, and of course the temperature of cleaning fluids, cleaning time and detergent solutions. With external cleaning however, you must consider much more, like: what kind of nozzle do I use? What spray angle? How many nozzles do I use? And how should the spray pattern move around the test object? We eventually managed to overcome all of these challenges by using an industrial robot arm that could perform a consistent, reliable, and reproducible test method.’
Tracy Schonrock, EHEDG Executive Committee member and Co-Chair of the EHEDG Sub-Committee Product Portfolio: ‘EHEDG has wanted to close this gap for a long time, but we had to make sure that we’d do it in the right way, and we finally did. Besides Fraunhofer IVV in Germany, the EHEDG Testing Laboratories ACTALIA in France, and Technology and Innovation Centre AINIA in Spain, will also start offering this new EHEDG testing service. We are aiming to roll out the OPC test method across more EHEDG Authorised Testing Laboratories around the world in the coming years.’
Best guarantee to be food contamination-free
Hygienic design contributes to effective food safety management. That is why food and beverage companies all over the world adopt hygienic design. It is also why regulatory and legislative bodies are now starting to include hygienic design in their food safety standards and prerequisite programs. The new hygienic design benchmarking requirements, issued by the Global Food Safety Initiative (GFSI), represent another step towards an industry-wide acknowledgement of the importance of hygienic design.
EHEDG plays a central role in this development. Over the course of decades, dozens of hygienic design guideline documents have proven to be fundamental for an effective testing and certification of food processing equipment. EHEDG Hygienic Design Testing and Certification basically defines which components may rightfully be labelled as hygienic design, and which may not. Therefore, a new EHEDG test method for open plant cleaning equipment is more than just another service that EHEDG offers to the industry - it is a first step that will ultimately result in the further adoption of hygienic design in all food processing environments by the entire global food processing industry.
Watch the interview with the Chair of the EHEDG Working Group Certification, Andrew Timperley.